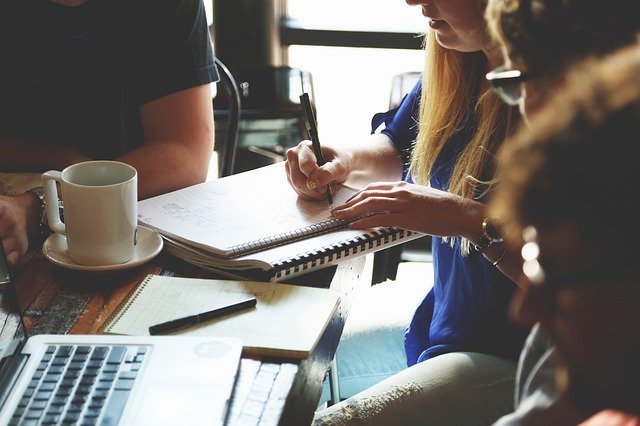
SPV, also known as a special purpose entity, is a subsidiary that helps a company minimize or isolate financial risks. This can be seen more easily in cases where the subsidiary may have a different liability than the parent company or if it invoices for services that may be hard for a third party to obtain. An SPV is formed using an operating agreement, which sets out how assets will be divided and liabilities are undertaken between the parent and its subsidiaries. Here are seven affordable ways you can use to manage your SPVs.
1. Condition Monitoring System
A condition monitoring system monitors the status of your facilities and equipment. In the case of SPVs, these systems can track an asset’s health. A condition monitoring system helps you know whether it is time to repair or replace a broken-down SPV. In some cases, information from a condition monitoring system may indicate that replacement is less expensive than repairs. This can help you decide whether to repair or replace your broken-down SPV.
2. Maintenance Planning
Maintenance planning is a way to save money by maintaining your plant’s assets. If you have an SPV, you can use maintenance planning to plan for repairs and replacements. The maintenance plan will help you predict the replacement and repair costs you may incur. For example, if your maintenance plan indicates that it will cost less to repair a broken-down SPV than to replace it, then you need only repair the broken-down SPV.
Preventive maintenance is keeping an instrument, system, or plant in a good state of repair by performing regular maintenance to prevent breakdowns and failures. In the case of an SPV, you could perform preventive maintenance at an interval of 500 cycles or 12 months of use.
3. Administration Software
If you have multiple SPVs, you can use software to help you administer them. This can help you manage resources, record transactions, and analyze status and performance. The software can also provide a database to store all the information gathered. Using the information, you can perform trend analysis and statistical analysis. This will help you see when it is time to replace an asset or change a process.
For instance, fund administration software can help you plan for funds periodically. With the information available in a database, you can analyze the funds and their usage to see whether they will be sufficient to meet your company’s needs. You can also analyze your fund’s performance to see how it is doing and make changes to improve it.
4. Improve Communication and Standardization
Communication is critical in an organization, especially when managing SPVs. The more you communicate, the better your information will be. If you have different systems or your communication tools are not standardized, your information may be incomplete or inaccurate. Communication can help you perform maintenance plans and send notifications to prospective customers. It also helps with operational efficiency, planning, and forecasting.
5. Software for Alarms, Monitors, and Event Logs
Using monitors, alarms, and event logs will help keep track of equipment status, which will help prevent losses caused by equipment failure. Using the software, you can ensure that the asset is working properly and ready for use.
Event logs record when who, and where the alarm was triggered. This information helps you track what triggered the alarm and when it occurred. You can use the data to identify operational issues and track down problems, which can help prevent future maintenance problems.
6. Spares Optimization
You can use spare optimization to reduce the spares you need if you have several SPVs. The process involves evaluating the current inventory and identifying items that are no longer needed or are outdated. This allows you to decide whether these items should remain in your inventory or be replaced with newer ones. The process also helps you identify potential risks and opportunities and whether other parts might work better than the spares.
7. Labeling
Labeling equipment is a way to communicate its functions and roles. The labels help you identify the equipment and its parts for maintenance, repair, or replacement. Labels may also help you identify the value of an asset if it sells.
Conclusion
In summary, there are many benefits to managing your SPVs effectively, such as keeping detailed asset information records, tracking trends regarding maintenance plans and funding management, and identifying potential risks or opportunities. All these benefits make it easy to manage your SPVs using the affordable ways discussed above.