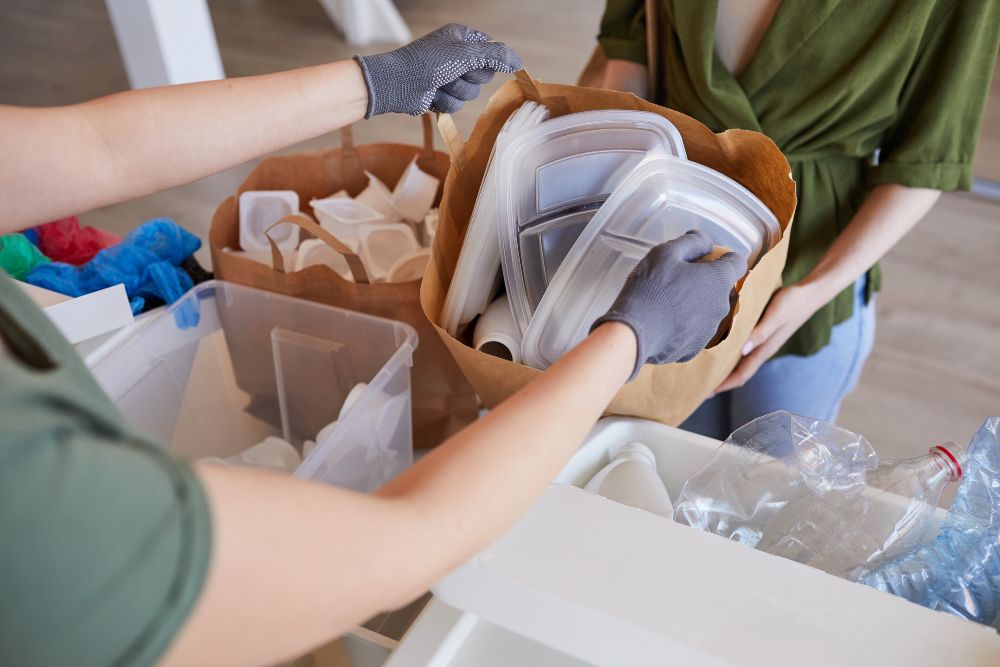
Every manufacturing plant produces some waste, that is just the nature of manufacturing. However, this waste can end up costing a business a lot of resources, which is why it is so important to establish guidelines that help minimize waste. Many of these guidelines fall under the principles of lean manufacturing, whose main aim is to keep costs low by reducing the different types of waste in manufacturing. So, how can manufacturers reduce wastage, especially as green manufacturing catches on?
Better Inventory Management
To reduce waste, manufacturers have to only order the materials they need for specific manufacturing processes and keep the right inventory levels. Doing both can reduce waste that is caused by damage, loss, and decay in storage and warehouses.
Reducing the amount of stored raw and hazardous material – which are sometimes necessary for some processes – can also help reduce the amount of waste generated.
Manufacturers have to also think about the wastage associated with warehousing. This can be labor, space, and the time it takes to locate products and materials in a disorganized warehouse. Better warehousing and only storing enough finished products to meet current and forecasted customer demands can help eliminate this issue or at least get it under control.
Do Regular Audits
Audits are crucial for understanding how equipment is being used and where improvements are required. An audit can catch equipment and tools that are failing or are about to fail, help remedy this situation, and thus prevent a breakdown that would lead to the wastage of time and money. These audits can also help extend the life of certain machines, saving manufacturing plants a lot of money in the future.
Audits also help reveal where additional employee and worker training is required. When workers use machines as they are not intended to be used, they expose these machines to greater wear, reduce their life spans, and increase the risk of them breaking down prematurely.
Lastly, audits reveal the risk current and future employee turnaround can bring to a business. If employees leave at the wrong time, that could have serious implications on not only productivity and output but also revenues. The data from the audit can help resolve any issues that would cause employees to want to leave.
Reduce Packaging Waste
In manufacturing, it is better to avoid an issue rather than try to rectify it when it has already happened. Managing both your packaging materials and processes is a great way to reduce wastage in this specific area.
When choosing materials, it is better to lean towards reusable and durable materials to prevent wastage. Also, manage the purchase of these materials carefully to ensure you are not buying more than you need at a time. This comes down to better purchase and inventory management.
Another way to reduce waste in packaging is to only use what is necessary and to encourage suppliers to also do the same on their end. Manufacturers can also redesign their packaging, so it uses the least amount of material possible.
Lastly, manufacturers can invest in better packaging machines. Modern machines are specifically made to reduce waste during the packaging process. For example, a modern cartoning machine will use the right carton forming guides to ensure the right carton size is used for the products being packaged. The Douglas cartoning machine is perfectly suited for different packaging sizes and applications while reducing waste. Douglas delivers cutting-edge, innovative, and precise packaging technologies and systems for different applications in various industries.
Use Recovery, Reuse, and Sorting Techniques
Manufacturing plants can use various techniques such as filtration, electrolysis, centrifugation, and reverse osmosis to revolve as much waste as they can from their different processes. Recycling is also a viable option, with materials like plastics, paper, and metal recycled regularly.
Manufacturing plants should refrain from recycling hazardous materials. In addition to being dangerous to all who handle them now and, in the future, there is often little economic benefit to doing so.
Sorting can help manufacturers know what waste they can reuse and what to throw out. This process can also be used as a part of the audit process where the plant looks at what it bins and sees where its waste is coming from.
Improve and Maintain
As with doing audits to prevent breakdown, maintenance and improvement are also crucial to reducing wastage. All manufacturers should invest in ensuring their machines are running as smoothly as possible.
Lubrication can save you a lot of time and prevent tear and wear, but too much of it can jam machines or contaminate products, both of which can lead to losses.
Wastage in production processes is not just about materials and products as it is also about other types of waste. These include time, money, labor, and other resources, and it is important to have guidelines and strategies in place to avoid wastage in all these areas.