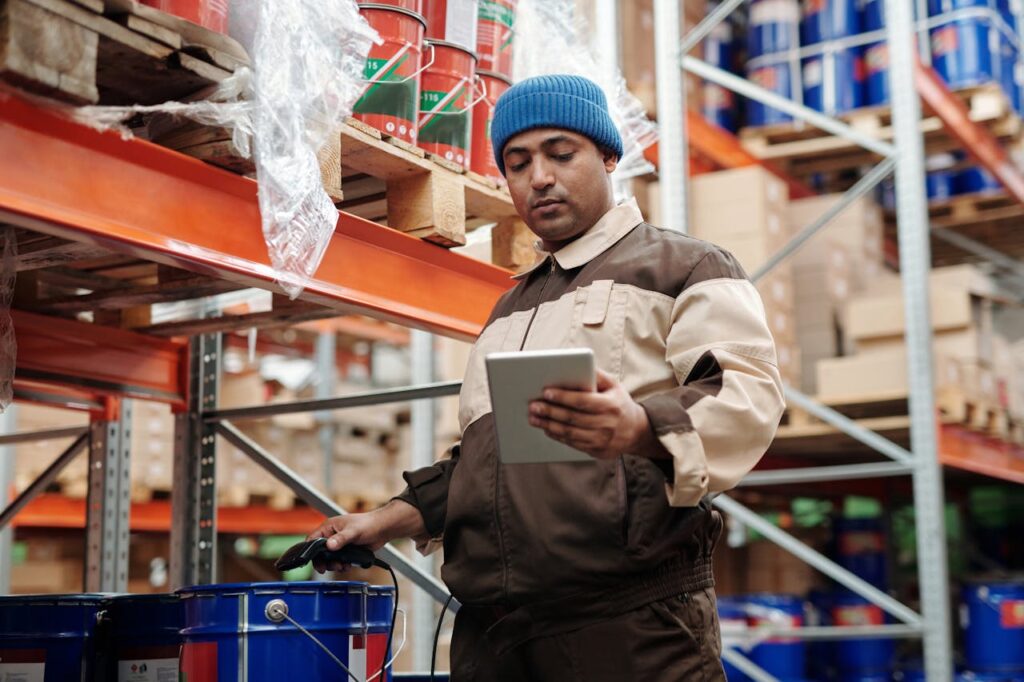
In today’s competitive market, maximizing production efficiency in a large warehouse is crucial for maintaining a strong supply chain and ensuring customer satisfaction. Efficient warehouse operations can lead to reduced costs, faster shipping times, and improved overall productivity. Here’s how you can achieve optimal production efficiency in a large warehouse setting.
Optimize Warehouse Layout
Designing an efficient warehouse layout is crucial for maximizing production efficiency. Start by organizing the warehouse to support a seamless flow of goods from receiving and storage to picking, packing, and shipping. Position high-demand items close to the shipping area to minimize the time spent retrieving them. Make use of vertical space by installing high shelving and mezzanine floors, which can expand storage capacity without increasing the warehouse footprint. Clearly marked pathways and signage help guide workers, reducing confusion and time spent locating items. Implementing a zone-based layout can further streamline operations by grouping similar items together. Regularly reassessing and adjusting the layout based on operational data can enhance efficiency, ensuring that the warehouse remains responsive to evolving demands and product mixes.
Leverage Technology
Investing in advanced technology can dramatically enhance warehouse efficiency. A Warehouse Management System (WMS) offers real-time insights into inventory levels, locations, and order statuses, streamlining processes and reducing errors. Automated Storage and Retrieval Systems (AS/RS) utilize robotics to handle goods, boosting speed and accuracy. Barcode and RFID systems improve inventory tracking, reducing discrepancies and enhancing stock management. Automated Guided Vehicles (AGVs) and Autonomous Mobile Robots (AMRs) transport goods within the warehouse, decreasing manual labor and accelerating operations. Embracing these technologies not only improves efficiency but also provides better scalability and flexibility to adapt to increasing demands and changing market conditions, ensuring long-term operational success.
Implement Lean Practices
Adopting lean practices focuses on eliminating waste and optimizing processes to boost efficiency. The 5S methodology—sort, set in order, shine, standardize, and sustain—maintains a clean and organized workspace, preventing errors and delays. Just-In-Time (JIT) inventory minimizes holding costs and ensures materials are available exactly when needed, improving flow and reducing waste. Encouraging a culture of continuous improvement, or Kaizen, involves regularly evaluating processes and implementing small, incremental changes suggested by employees. This proactive approach leads to ongoing enhancements in productivity and quality, creating a workplace environment that continually strives to improve efficiency and eliminate unnecessary steps.
Enhance Employee Productivity
Maximizing employee productivity is vital for achieving warehouse efficiency. Providing comprehensive training ensures that workers are skilled in using equipment and following procedures, which reduces mistakes and increases speed. Ergonomically designed workstations and tasks minimize physical strain and fatigue, enhancing comfort and productivity. Implementing incentive programs can motivate employees to reach higher performance levels, fostering a sense of accomplishment and dedication. Cross-training employees for multiple roles adds flexibility, allowing the warehouse to adapt to varying workloads and staff shortages. By investing in the workforce through training, ergonomic improvements, and motivational incentives, warehouses can create a productive and efficient operational environment, leading to better overall performance.
Improve Inventory Management
Effective inventory management is essential for maintaining smooth warehouse operations. Utilizing ABC analysis helps prioritize high-value and fast-moving items, ensuring they are readily available and accurately tracked. Regular cycle counting keeps inventory levels accurate without the need for complete shutdowns, quickly identifying and correcting discrepancies. Advanced demand forecasting techniques use historical data and market trends to predict future needs, optimizing stock levels and reducing the risk of overstocking or stockouts. Maintaining precise inventory records and aligning stock with demand helps improve order accuracy, enhances customer satisfaction, and reduces holding costs. These practices collectively contribute to overall efficiency and a more responsive supply chain.
Streamline Order Fulfillment
Efficient order fulfillment processes are crucial for fast and accurate deliveries. Batch picking consolidates similar orders, reducing travel time and increasing efficiency. Wave picking organizes orders based on shipping schedules and priorities, balancing workloads and ensuring timely processing. Pick-to-light and voice-picking systems guide workers through tasks with visual or audio cues, reducing errors and speeding up operations. Integrating these techniques enhances the speed and accuracy of order fulfillment, resulting in faster shipping times and improved customer satisfaction. Continuously monitoring and optimizing these processes ensures that the warehouse can handle high volumes efficiently, adapting to fluctuations in order patterns and customer demands. This adaptability is key to maintaining high performance in a dynamic market.
Conclusion
Maximizing production efficiency in a large warehouse requires a comprehensive approach that includes optimizing the layout, leveraging technology, implementing lean practices, enhancing employee productivity, improving inventory management, streamlining order fulfillment, maintaining equipment, and continuously monitoring performance. By adopting these strategies, warehouses can achieve higher productivity, reduce costs, and enhance overall operational efficiency.