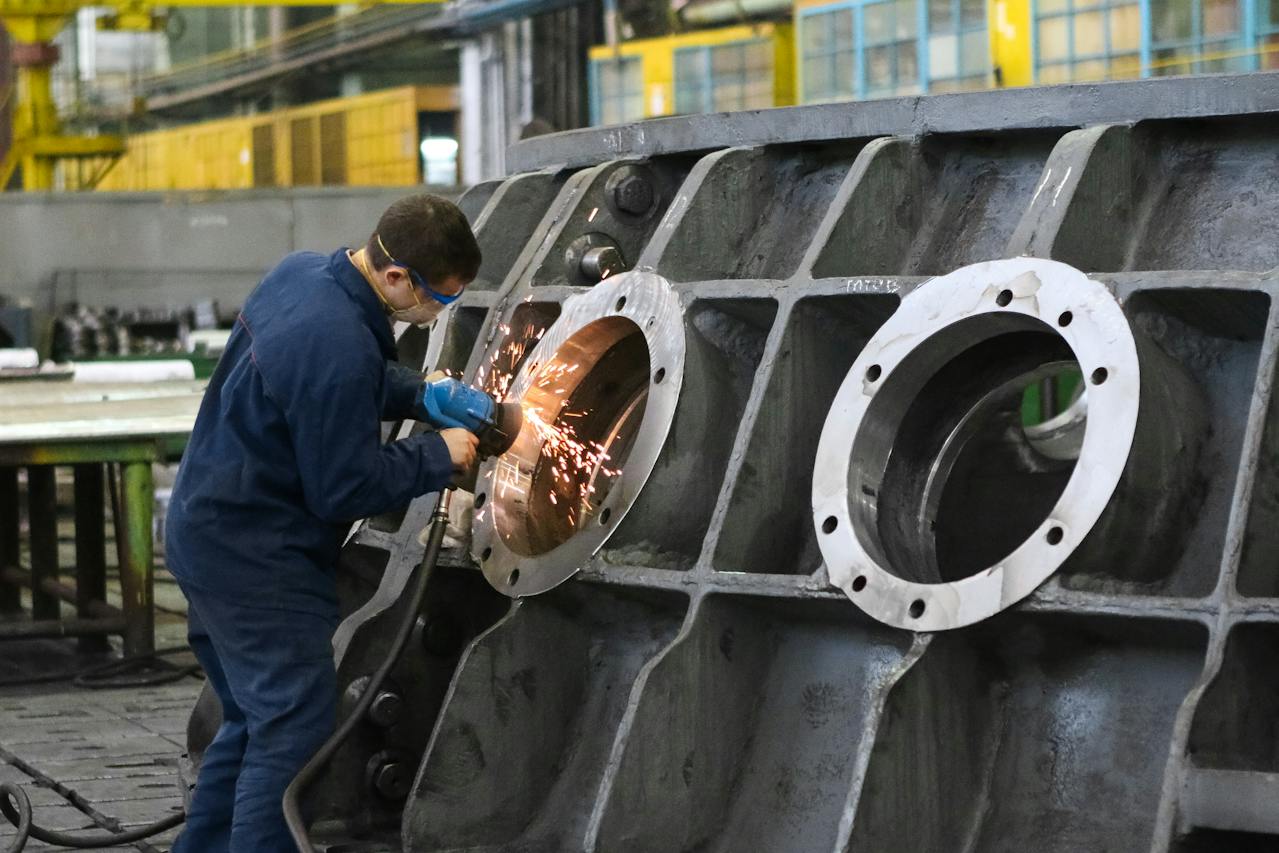
In the dynamic and fast-paced realm of manufacturing, ensuring the safety of workers is of utmost importance. The implementation of effective safety procedures not only safeguards employees but also contributes to heightened productivity and operational efficiency. Here are five pivotal strategies to augment safety procedures within a manufacturing facility.
Holistic Training Initiatives
Foundational to cultivating a robust safety culture in a manufacturing facility are comprehensive training programs. These programs should encompass various facets, including the operation of machinery, emergency response protocols, and the correct utilization of personal protective equipment (PPE).
Enrolling in core tools training courses empowers manufacturing professionals with the essential skills and methodologies needed to elevate quality standards, enhance process efficiency, and drive continuous improvement within their respective industries.
Continuous and regular training guarantees that employees stay updated on the most recent safety standards and adhere to best practices. Training initiatives should extend beyond the initial onboarding phase with periodic refresher courses.
Additionally, hands-on exercises and simulations can offer practical experience, enabling employees to adeptly respond to potential hazards. By investing in continuous education, manufacturing facilities empower their workforce to make informed decisions in high-pressure situations, thereby reducing the risk of accidents.
Ergonomic Design and Optimization of Workstations
Ensuring workstations boast an ergonomic design is paramount to mitigating the risk of musculoskeletal disorders and enhancing overall worker well-being. The implementation of ergonomic principles involves a thorough assessment and adjustment of workstation layouts, the provision of ergonomic tools and equipment, and the promotion of proper body mechanics.
By optimizing workstations to alleviate physical strain and discomfort, manufacturing facilities can enhance employee health, prevent injuries, and significantly boost overall operational efficiency.
Incorporating regular ergonomic assessments and soliciting employee feedback further ensures a continually evolving and responsive approach to workstation optimization, fostering a workplace environment that prioritizes both health and productivity.
Emergency Response Drills and Readiness
Beyond regular safety training, manufacturing facilities should conduct frequent emergency response drills to prepare workers for potential crises. These exercises replicate diverse situations, including fires, chemical spills, or equipment malfunctions, allowing employees to rehearse their responsibilities and become acquainted with emergency protocols. Regular drills not only improve the effectiveness of response efforts but also instill confidence in employees, ensuring a swift and coordinated reaction in the face of unforeseen events.
Additionally, the debriefing sessions following these drills provide valuable insights, allowing organizations to refine emergency protocols, identify areas for improvement, and enhance overall preparedness for a wide range of potential incidents. Continuous evaluation and adaptation based on these insights further strengthen the facility’s resilience against unforeseen challenges.
Clear and Prominent Signage
Effective communication is paramount in a manufacturing environment, and clear, visible signage plays a crucial role in guiding employees and visitors safely through the facility. Well-placed signs indicating emergency exits, hazardous areas, and safety protocols serve as constant reminders of necessary precautions.
Investment in high-visibility signage and ensuring it stays up-to-date contribute to a safer work environment by reducing the likelihood of accidents caused by confusion or lack of awareness. Regular evaluations of signage effectiveness and employee feedback mechanisms further enhance communication strategies, ensuring continuous improvement in safety communication practices.
Additionally, fostering a culture that encourages employees to actively engage in safety discussions can lead to valuable insights, making safety communication a collaborative effort that promotes a culture of shared responsibility and awareness.
Support Programs for Mental Health
Recognizing the significance of mental health in the workplace is growing increasingly imperative. Manufacturing facilities should implement support programs addressing the psychological well-being of their workforce. High-stress environments and demanding production targets can impact mental health, potentially leading to accidents and decreased productivity.
Providing counseling services, organizing workshops on stress management, and advocating for a positive work-life balance collectively contribute to cultivating a healthier and more robust workforce.
Taking proactive measures to address mental health not only enhances employee satisfaction but also diminishes absenteeism, fostering an inclusive workplace culture that prioritizes the overall well-being of each team member. Employers who prioritize mental health demonstrate commitment to employee welfare and overall organizational success.
Conclusion
emphasizing ergonomic design, frequent emergency response drills, clear signage, mental health support, and continuous improvement through data analysis collectively strengthen safety measures in manufacturing. These practices not only improve worker well-being but also contribute to a durable and efficient operational setting, guaranteeing ongoing safety enhancements.