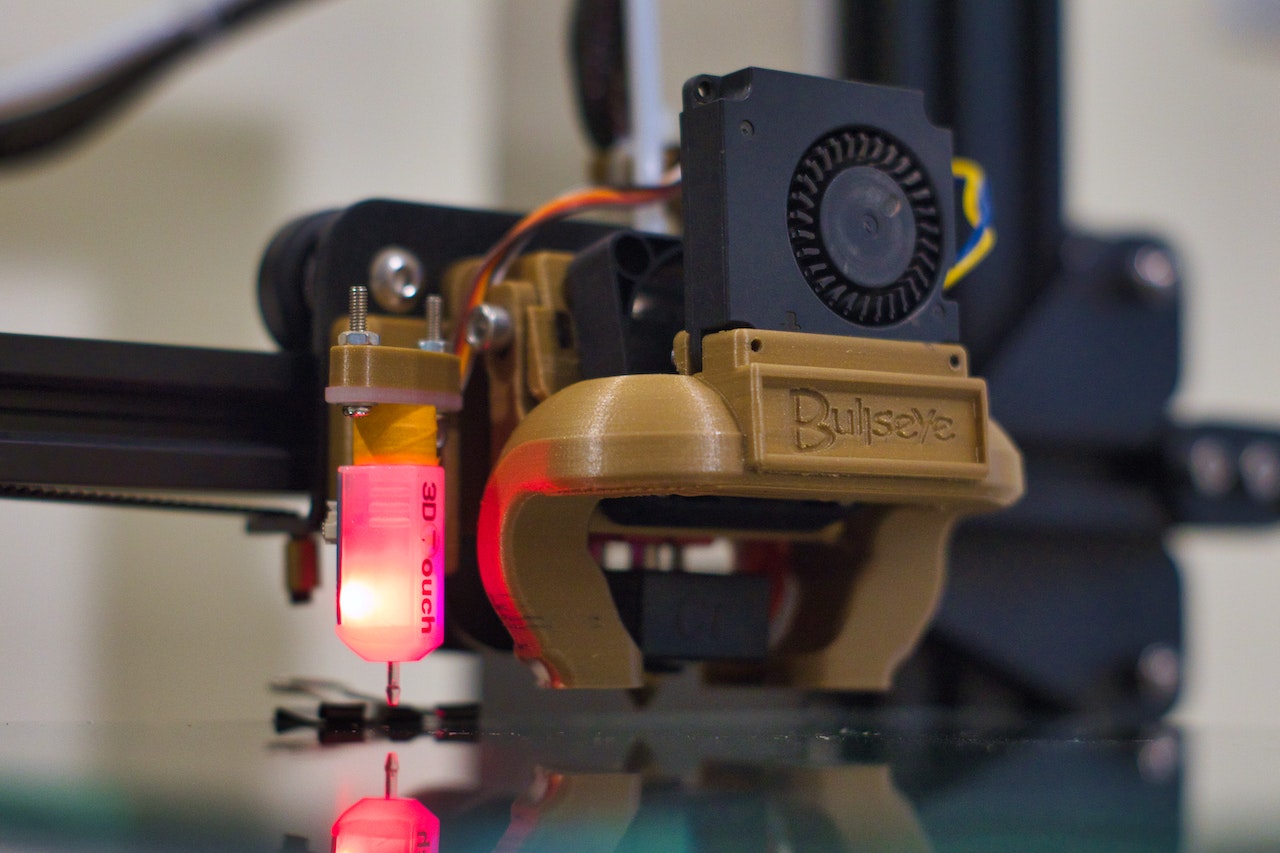
In the manufacturing industry, efficiency is the cornerstone of success. As industries evolve and competition intensifies, organizations are constantly seeking ways to streamline processes and deliver exceptional results. To help your company find answers, here are five innovative manufacturing solutions that can revolutionize project efficiency. From embracing automation and data-driven insights to fostering a culture of continuous improvement, these strategies empower manufacturers to elevate their operations and achieve new levels of productivity.
Automation and Robotics Integration
Integrating automation and robotics technology is a game-changer for manufacturing efficiency. By automating repetitive tasks through CNC turning services, organizations reduce human intervention, minimize errors, and enhance production speed. Robotics excel in precision tasks, such as assembly and quality control, where consistency and accuracy are paramount. With the ability to work around the clock, automation optimizes resource utilization, allowing employees to focus on more complex and value-added activities.
Robotics offer the flexibility to adapt to varying production demands, making it easier to scale operations when necessary. The integration of automation not only accelerates project timelines but also improves overall quality, creating a manufacturing environment that thrives on efficiency and innovation. Embracing automation can lead to improved product consistency, reduced lead times, and enhanced workplace safety.
Data-Driven Insights and Analytics
Harnessing the power of data-driven insights is essential for informed decision-making and project optimization. By implementing advanced analytics and machine learning algorithms, manufacturers gain a comprehensive understanding of their processes, identifying bottlenecks and areas for improvement. Real-time data enables proactive maintenance, reducing downtime and maximizing equipment uptime.
Furthermore, predictive analytics forecast demand patterns, enabling organizations to optimize inventory levels and reduce waste. By leveraging data-driven insights, manufacturers fine-tune operations, minimize inefficiencies, and align their strategies with market trends, driving continuous improvement and competitive advantage. Data-driven insights can also provide valuable insights into customer preferences and behaviors, allowing manufacturers to tailor their products and services to meet evolving demands.
Lean Manufacturing Principles
Adopting lean manufacturing principles is a timeless strategy for enhancing efficiency. This methodology emphasizes waste reduction, efficient resource utilization, and continuous improvement. By identifying and eliminating non-value-added activities, manufacturers streamline workflows, optimize material usage, and reduce lead times. Lean practices also promote standardized work processes, ensuring consistency and minimizing variations in output.
The implementation of visual management tools and standardized work instructions further enhances clarity and efficiency on the shop floor. Embracing lean principles empowers manufacturers to achieve higher productivity, reduced costs, and enhanced customer satisfaction. Implementing a 5S system (Sort, Set in order, Shine, Standardize, Sustain) as part of lean manufacturing can result in a more organized and efficient workspace, contributing to improved overall operations.
Advanced Supply Chain Management
Efficient project execution relies on a well-orchestrated supply chain. By leveraging advanced supply chain management tools, manufacturers optimize inventory levels, reduce lead times, and enhance communication with suppliers. Collaborative platforms facilitate real-time sharing of information, enabling swift responses to changes in demand or supply chain disruptions. Implementing just-in-time (JIT) manufacturing principles minimizes inventory holding costs while ensuring timely availability of materials.
Moreover, supply chain analytics provide visibility into supplier performance, allowing manufacturers to make informed sourcing decisions. A robust supply chain management strategy enhances project efficiency by ensuring seamless material flow and minimizing production delays. Establishing strong relationships and partnerships with key suppliers can further enhance supply chain efficiency and flexibility.
Continuous Improvement Culture
Fostering a culture of continuous improvement is fundamental to sustained manufacturing efficiency. Organizations that encourage employee engagement and empowerment in process optimization reap significant benefits. By soliciting employee input, manufacturers tap into valuable insights for streamlining operations, enhancing product quality, and reducing waste. Regular training and skill development programs keep employees updated on industry trends and best practices, contributing to a highly skilled workforce.
Additionally, recognizing and rewarding innovative ideas incentivizes employees to contribute to process enhancement. A culture of continuous improvement nurtures an environment where efficiency is valued and embraced as a collective effort. Encouraging cross-functional teams and brainstorming sessions can further foster a culture of innovation and continuous improvement.
Bottom Line
In the manufacturing industry, efficiency isn’t just a goal; it’s a driving force that shapes competitiveness and success. By embracing automation, leveraging data-driven insights, adopting lean principles, optimizing the supply chain, and fostering a culture of continuous improvement, manufacturers empower themselves to optimize project execution and deliver superior outcomes. As the industry continues to evolve, these solutions serve as beacons of progress, guiding organizations toward an era of heightened efficiency, innovation, and sustained growth. By embracing these solutions and fostering a culture of innovation, manufacturers position themselves for long-term success in an ever-evolving landscape.