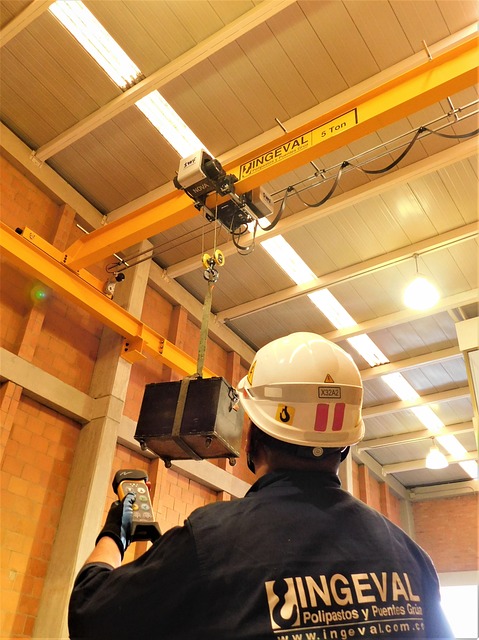
Ensuring the safety of workers is of paramount importance when it comes to operating overhead cranes. While these machines significantly enhance productivity in various industries, they also come with inherent risks. To safeguard employees and create a secure work environment, it is essential to implement effective safety measures. This article presents a comprehensive set of tips and recommendations for operating overhead cranes safely. By following these guidelines, companies can protect their workers from potential accidents and foster a culture of safety and well-being in the workplace.
How to Ensure the Safety of Your Employees When Using an Overhead Crane?
Comprehensive Training and Certification
Crane operators must be trained in operating procedures, safety standards, and emergency response. Operators should learn how to operate the crane and why certain procedures are important via theoretical and practical training. Load balance, crane capacity, preventative maintenance, and safety device use can be covered.
The National Commission for the Certification of Crane Operators (NCO) in the U.S. or comparable agencies in other countries shall certify operators. This certification proves the operator’s crane operating competence and meets a national requirement. Your company’s safety culture should include regular refresher training and recertification to keep operators up to speed with safety standards and equipment advancements.
Regular Equipment Inspections
The crane and its equipment must be inspected regularly for safe and effective operation. Preventive maintenance checks beams, hooks, and cables for wear, distortion, and damage. Controls and lifting mechanisms should be tested for responsiveness and accuracy.
To make sure limit switches, brakes, and locking mechanisms operate properly, examine them. Regular inspections avoid major damage and extend the crane’s lifespan by finding and fixing problems early. Remember, an undiscovered little problem might develop into a big malfunction, which could endanger safety and disrupt operations. Thus, maintaining a safe and productive workplace requires a thorough and frequent inspection routine.
Proper Load Handling
Accidents frequently occur due to overloading, which can result in collapses or sudden drops in the load. For instance, if a 10-ton overhead crane is used beyond its maximum weight capacity, it can have disastrous consequences. Following the crane manufacturer’s maximum load capacity is crucial.
Overloading the crane might destroy its structure. Before lifting, the load must be equally distributed and firmly connected to the crane’s hook. Uneven loading might tilt or swing the crane, causing significant accidents.
Experienced workers utilizing slings or chains should assess load stability. These steps secure and balance the burden. An overhead crane operator should be educated to notice and react to overloading indicators, including strange sounds, excessive sway, or lifting problems. Stop operations, gently decrease weight, and notify supervisors in such cases.
Clear and Safe Operating Area
Operators and other workers must have a clear, safe working space around the crane. To eliminate impediments, assess the work area. This might include loose materials, equipment, or other dangers that could disrupt crane operation or cause tripping risks.
Mark the operational area with signs, cones, or barriers. The crane’s swing radius and load transit zones should fit within this delineation. This area should be off-limits to unauthorized individuals during crane operations to minimize crane collisions and falling debris.
All site workers should learn about these defined zones and the need to keep a safe distance during crane operations. Regular safety briefings can reinforce this message and answer questions. Maintaining a clear and safe operating space reduces accident risk and makes the workplace safer.
Regular Maintenance and Repairs
Maintenance is essential for overhead crane safety and efficiency. Preventative maintenance should follow manufacturer and industry guidelines. This program should include frequent inspections, lubrication, and safety device and control testing.
Repair or replace worn, damaged, or malfunctioning components immediately. Qualified technicians must execute these maintenance activities and repairs. These experts can spot problems and fix them securely.
Regular maintenance extends equipment life and prevents expensive downtime while guaranteeing crane safety. Preventing breakdowns and safety incidents requires proactive maintenance. Maintaining cranes regularly and thoroughly ensures their long-term productivity and safety.
Emergency Preparedness
When working with huge gear like overhead cranes, emergency preparation is essential. Emergency protocols must be well-communicated. These processes should include shutting down the crane if it malfunctions, evacuating personnel in a major incident, and treating any injuries.
All staff—not just crane operators—must understand these processes. Drills can assist everyone in knowing what to do and where to go in an emergency. These exercises test processes and detect and fix problems.
First aid supplies, fire extinguishers, and safety alarms are also needed. Prepare for crises this way to guarantee a quick and efficient reaction that minimizes hurt and damage.
Encourage a Culture of Safety
Workplace safety is essential to worker well-being. This is critical in a crane-operated setting. Workers feel responsible for their and their coworkers’ safety in this culture.
Workers should be encouraged to report safety issues. This can need a clear reporting procedure and no consequences for those reporting issues. Safety measures must be followed regardless of manufacturing schedules.
Safety culture requires continuous learning. This might include safety briefings, continuing training, and safety rules and equipment technology updates. A robust safety culture that reduces accidents boosts worker morale, productivity, and quality.
Conclusion
During the operation of an overhead crane, one of the most important responsibilities is to protect the safety of the workers. Businesses are better positioned to safeguard their employees and reduce hazards if they provide extensive training, do routine equipment inspections, appropriately manage loads, keep the working area clean, engage in routine maintenance, plan for potential crises, and cultivate a safety culture. Remember that safety is not only a set of guidelines; it is an essential principle permeating all facets of crane operation. Businesses can maintain a productive and secure working environment where every worker is protected and every lift counts, provided they make worker safety a priority and make it a top priority. Therefore, safety stands tall as the beacon of efficiency in the realm of overhead crane operation. It guides operations toward success while safeguarding the well-being of every worker participating in the process.