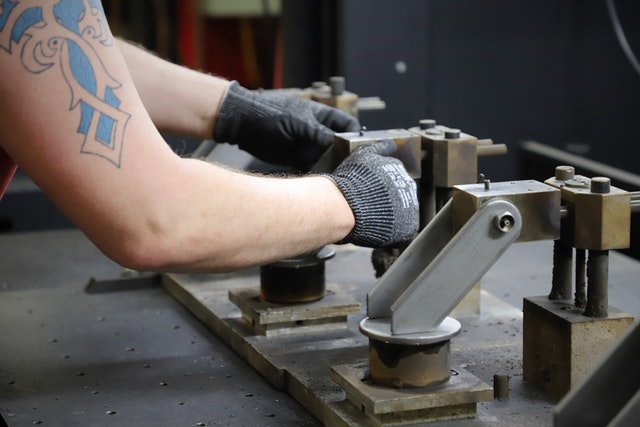
An unexpected manufacturing breakdown can cause serious disruption and wreak havoc on production. Unfortunately, it’s all too easy for these breakdowns to happen—especially if preventive maintenance and monitoring aren’t given enough attention. The good news is that with a little extra effort, manufacturers can identify potential problems before they occur. Here’s how.
Utilize Predictive Maintenance Strategies
Predictive maintenance is a strategy based on monitoring and data analysis that enables manufacturers to anticipate when their equipment will need servicing or repair. By taking advantage of predictive maintenance strategies, companies can avoid unexpected downtime due to equipment failure and reduce costs associated with preventable repairs and replacements. A few ways companies can leverage predictive maintenance include:
• Measuring vibration readings on critical assets
• Monitoring lubricant levels in moving parts
• Utilizing Thermography to detect temperature changes in assets
• Inspecting key components visually or using an endoscope camera
Analyze Data From Equipment Sensors
Equipment sensors can provide valuable data about the performance and usage of machinery. This data can help you learn more about how your equipment is functioning and understand which parts may need service or maintenance. By using data from equipment sensors, you can better understand the overall health and operation of your machines and identify any potential issues that may arise. Additionally, analyzing this data can provide insight into use patterns and inform decisions about when to schedule component maintenance or replacements. With the proper analysis tools and techniques, you can make informed decisions about how best to manage your equipment.
Analyzing data from equipment sensors allows you to see a comprehensive view of how each part of your equipment is functioning. By understanding this data, you can assess the overall performance of your machinery and make any necessary adjustments. Additionally, it allows you to optimize resources by determining when parts need service or replacement.
Via Pexels
Keep Track of Historical Maintenance Records
In addition to analyzing data from equipment sensors in real-time, manufacturers should also track historical maintenance records for each piece of equipment in their factory. This information can help them spot patterns in terms of when certain pieces of equipment are most likely to break down or require servicing so they can plan ahead and proactively address issues before they become significant problems. Additionally, having access to this information makes it easier for manufacturers to compare the performance of different pieces of equipment over time so they can more accurately assess which pieces are most reliable and cost-effective in the long run.
Regularly Review Operating Procedures
Manufacturers should also take the time to review their operating procedures periodically to identify any potential risks or areas where improvements could be made that would reduce the likelihood of a manufacturing breakdown occurring in the future. This could involve anything from changing out worn parts more frequently, adjusting speeds on certain machines, tightening up safety protocols and procedures, etc., all depending on the particular needs of each manufacturer’s operations.
Analyzing data from equipment sensors can help manufacturers gain valuable insight into the performance and usage of their machines. This information can be used to identify potential issues before they become more serious and inform decisions about when and how often certain pieces of equipment should be serviced or replaced. Additionally, keeping track of maintenance records and regularly reviewing operating procedures are necessary steps for avoiding costly breakdowns in the future. By taking these steps, manufacturers will better understand their equipment’s functionalities and be able to make informed decisions that will maximize efficiency and reduce downtime.